Fabrication
Coutellerie Au Sabot masters every step of the knife manufacturing process at its workshops. There are over 40 steps that have to be worked to make a knife. Certain steps are carried out on a machine, others entirely by hand. Below is a list of the main steps:
Cutting
The first operation involves shaping the knife’s various components. The cutler does this using a hole puncher, referred to as a die in the cutlery industry. This operation is carried out manually by an operator who guides the steel strip as it passes through the machine. The cutting operation can also be carried out using a laser cutter, i.e. a computer-controlled machine that guides a laser beam. This beam provides highly accurate blade cutting.
Grinding
The blade is ground to give it the shape required to achieve its cutting edge. This operation is carried out in two stages: the first stage follows the cutting operation and is to thin the blade; the second stage comes after straightening, and provides the final bevel and refines the cutting edge. The cutler needs to use all their extensive experience to carry out this step. Formerly carried out using whetstones, nowadays blades are ground on special machines that require perfect control by the cutler.
Hand-chiselling the spring
The spring is the central part of the handle that controls the blade’s opening and closing mechanism. Hand-chiselling involves decorating the back of the spring with sunken designs. Depending on the desired result, this operation is carried out using a file, or a whetstone or on a machine.
Assembly
Once all the components are completed, they can be assembled to form the knife. This is a fiddly, painstaking operation as the various parts have to be assembled and adjusted manually with the greatest care and precision. Adjusting the handles, drilling, assembling the sections on the plates… it can take an operator years to build up the experience necessary to achieving the perfect touch.
Technical vocabulary
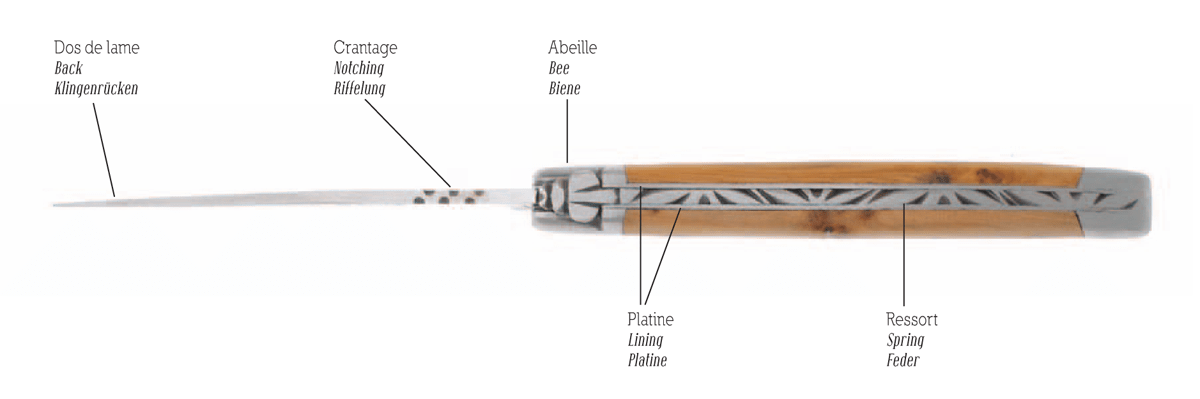
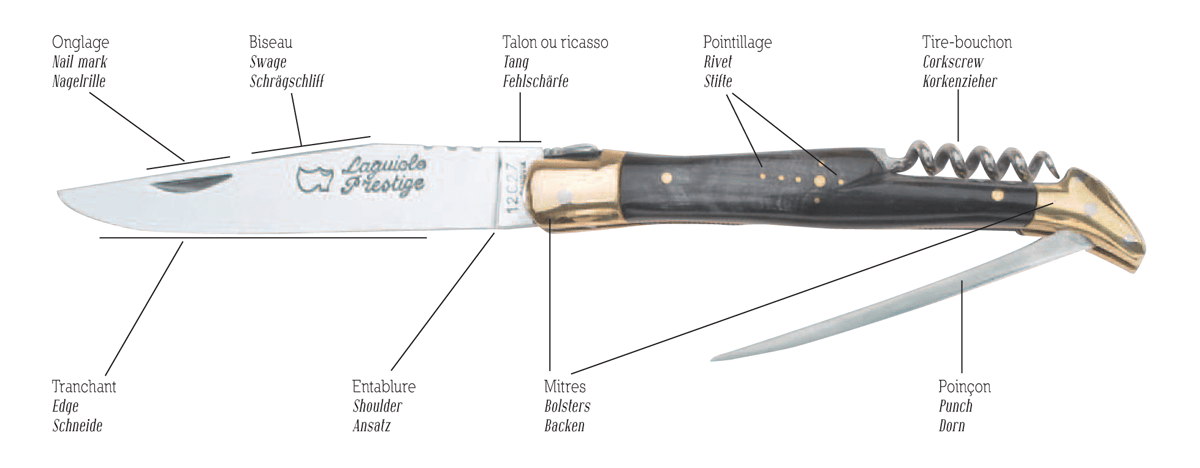